At Stream Design, we take immense pride in our state-of-the-art infrastructure, which forms the backbone of our high quality decorative plywood production. Our advanced manufacturing facilities seamlessly blend cutting-edge technology with traditional craftsmanship, enabling us to create products that meet the highest industry standards. Each element of our infrastructure is meticulously designed to enhance efficiency and ensure that every sheet of veneer reflects our commitment to excellence.
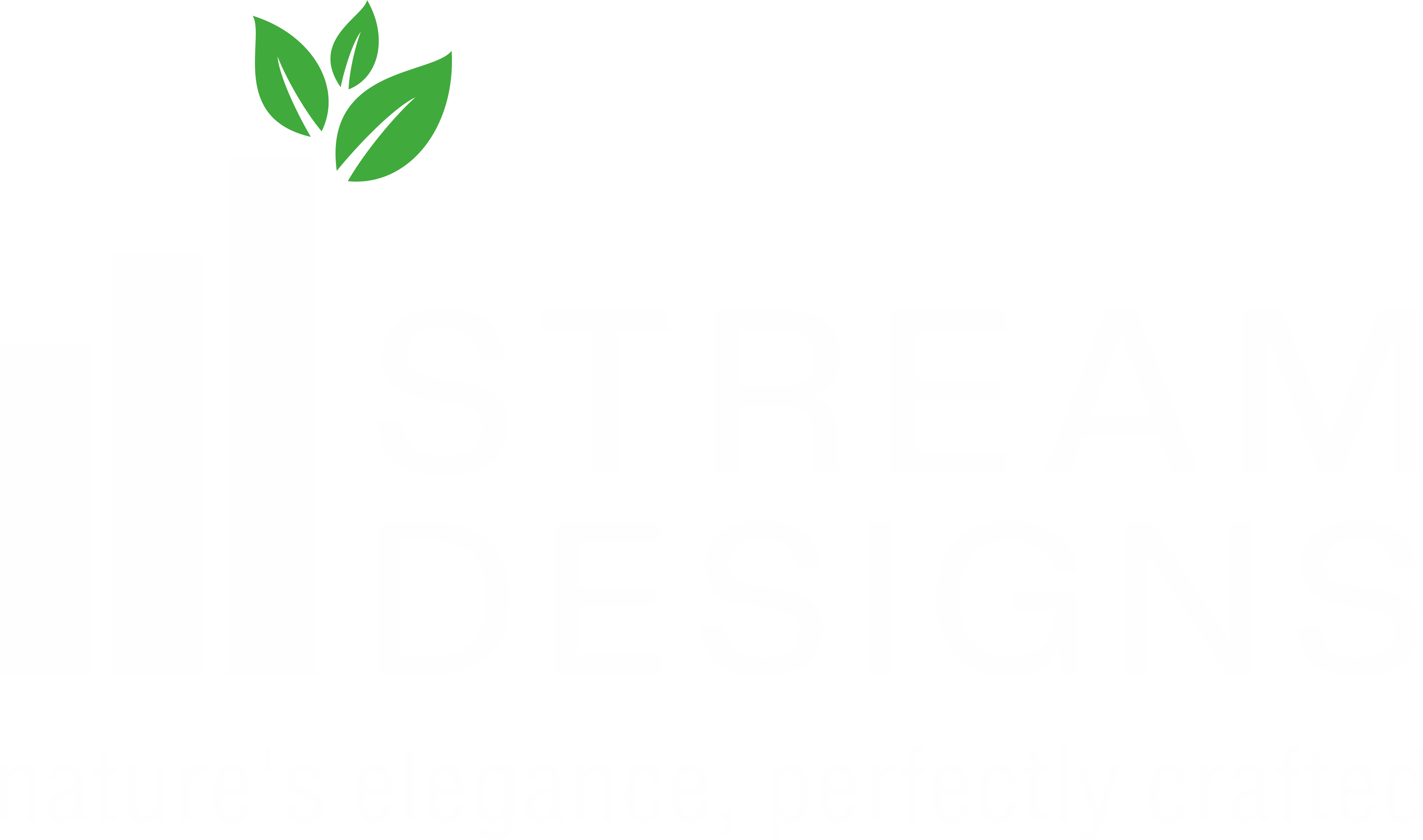